Digital Transformation
Put your people in control of how their work gets digitised
Zaptic’s no code approach accelerates shop floor digitalisation without expensive changes to equipment processes.
Request Demo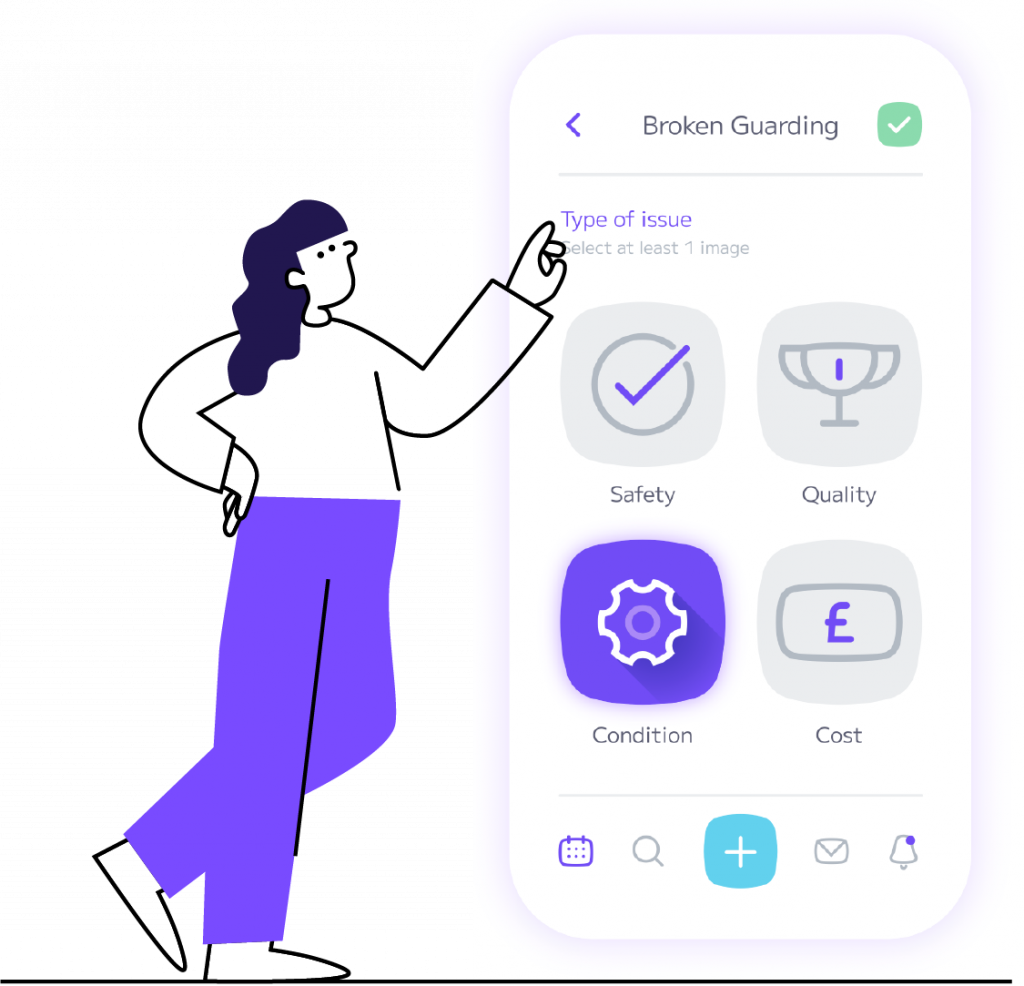
The Problem
Our Solution
Digital manufacturing leaders recognise that a smart factory is not so smart without connected workers. After all, what is the use of big data and analytics if people still work with paper and spreadsheets?
In a market crowded with marketing hype and incumbents which continue to struggle to provide a truly user friendly experience, the challenge is selecting the right partner and avoiding slow, costly failed experiments.
Zaptic provides a no code toolkit designed specifically to digitise operations for frontline workers.
This gives control to the people closest to problems to create solutions quickly, in an agile and user validated way, supported by an enterprise grade platform with flexible integrations to core IT systems. The result is not just faster digitisation, but strong, user led adoption and results.
How Zaptic Helps
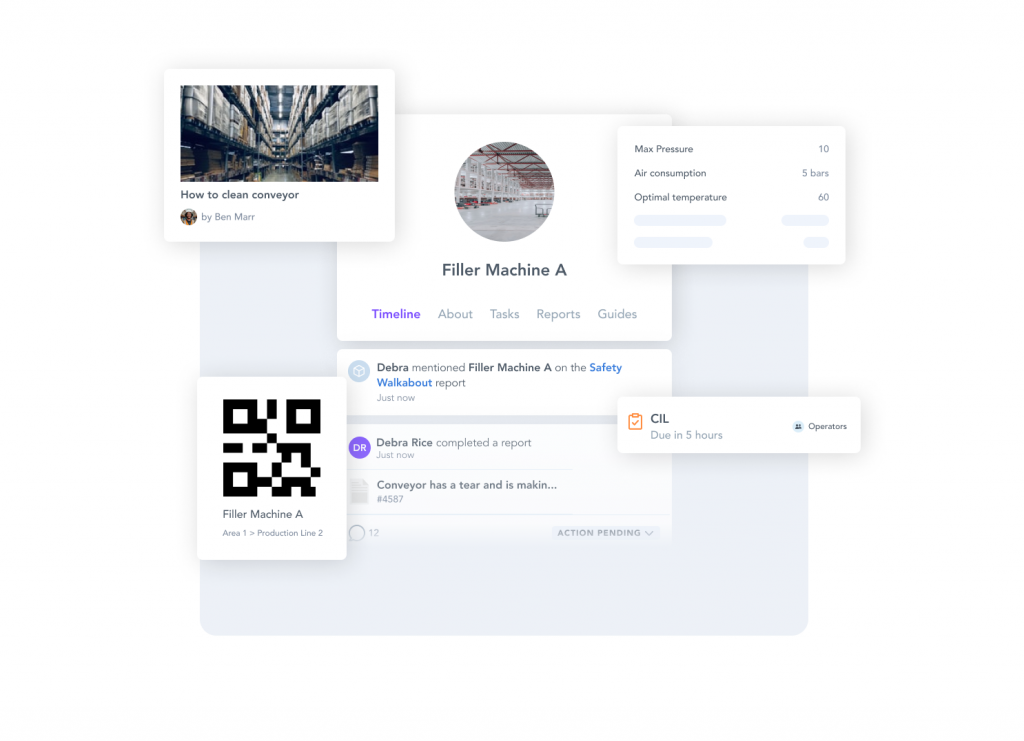
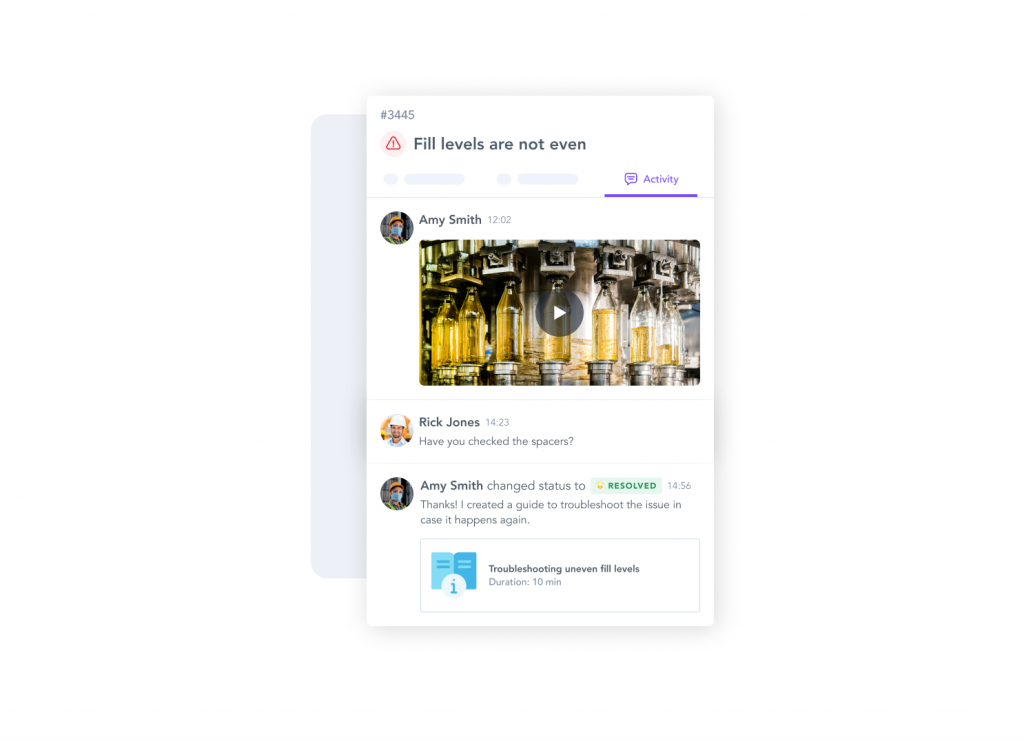

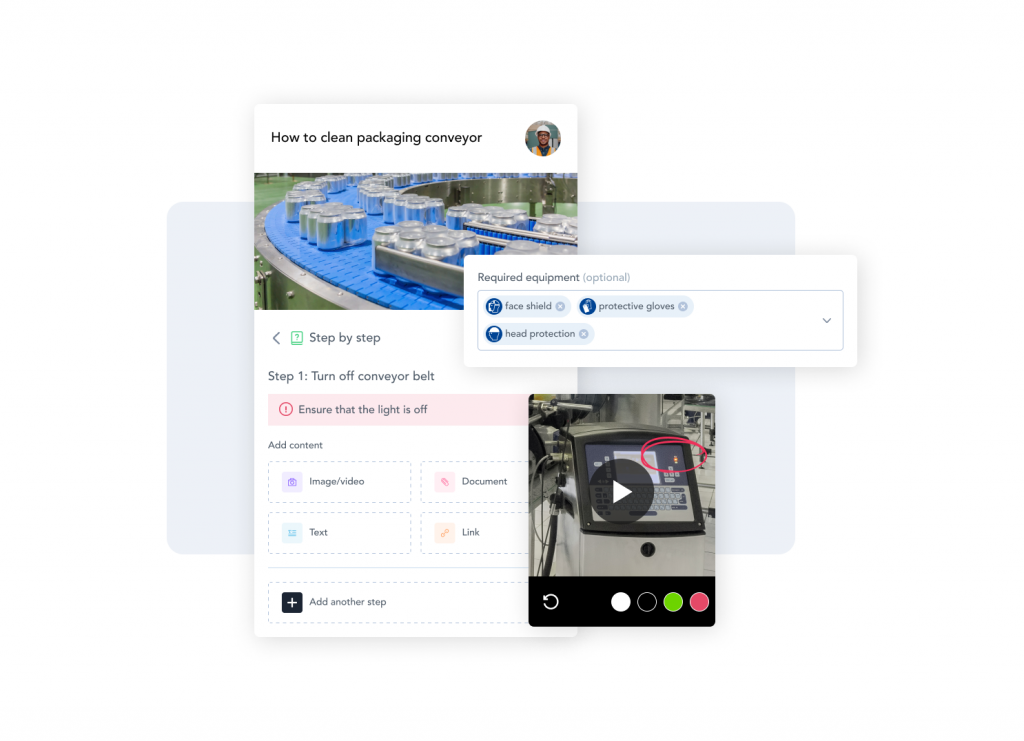
Operator Autonomy
On the floor access to work instructions via scan or search within the connected worker solution.
Capture and escalate defects with rich media directly from the place of work.
Integrate with machine and production data (e.g. MES, historian), to push the right checks and work instruction, to the right user, at the right time.
Shop Floor Collaboration
Capture, visualise and track all issues and actions on Zaptic’s daily management boards to aid communication between shifts and speed up problem solving with electronic work instruction.
Event based communication streamlines collaboration between production teams and support functions to aid troubleshooting, repairs and day to day problem solving.
Build escalations workflows to automate, streamline and standardise issue resolution cycles.
Process Traceability
Digital workflow timelines provide visibility on what’s been done, by who and when, with conversation history and multimedia.
Process metrics and analytics boards highlight improvement and savings opportunities.
Automated audit trails ease inspection preparedness.
Knowledge & Best Practice Sharing
Deliver work instruction to workers in the flow of their work, by linking guides to digital workflows.
Capture, retain and organise knowledge by enabling workers to create guides (e.g. OPLs, troubleshoots etc) in an easy, social media style experience directly from the place of work.
A searchable database of previously resolved issues supports workers encountering similar issues, and promotes process standardisation.
The Results
The Results
9
Months To Go Paperless in DMS
Months To Go Paperless in DMS
250
Paperwork Hours Saved Per Week Per Site
Paperwork Hours Saved Per Week Per Site
11%
Overall Equipment Effectiveness improvement
Overall Equipment Effectiveness improvement
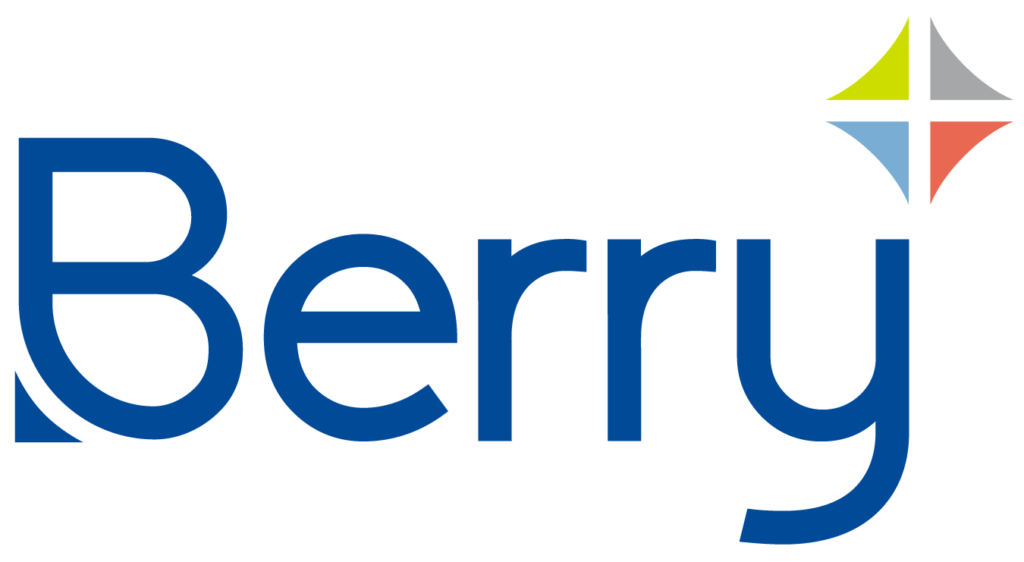
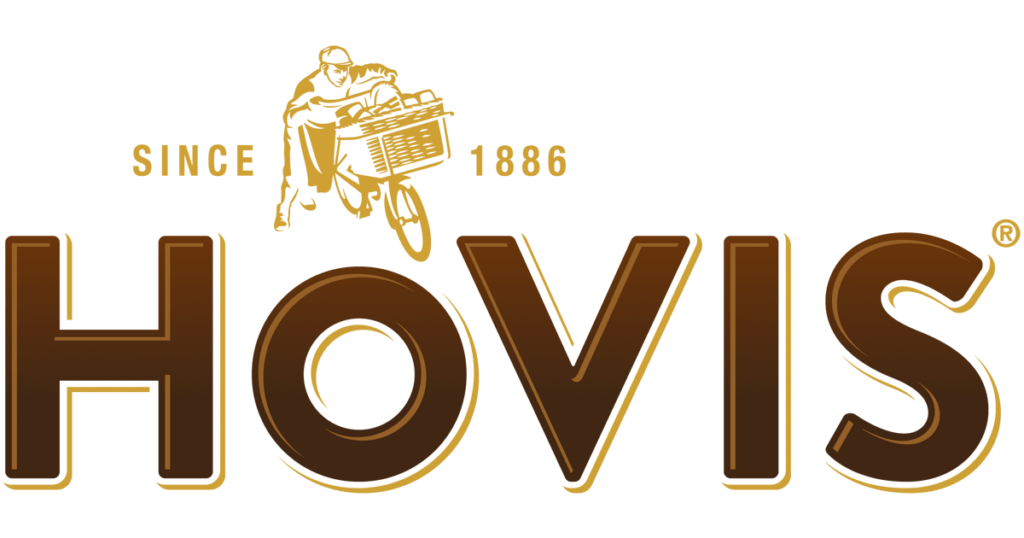

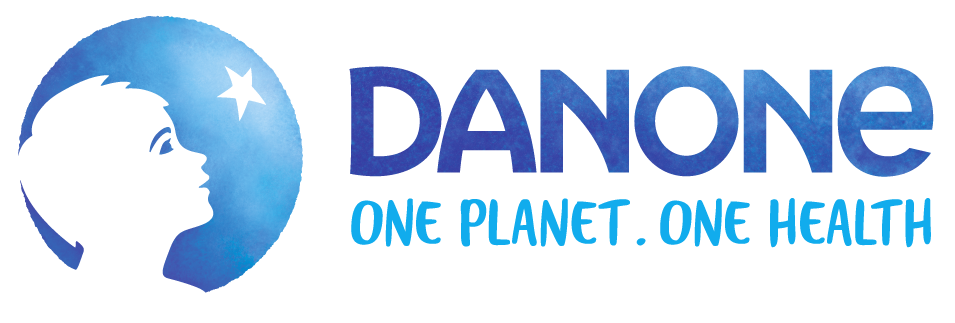
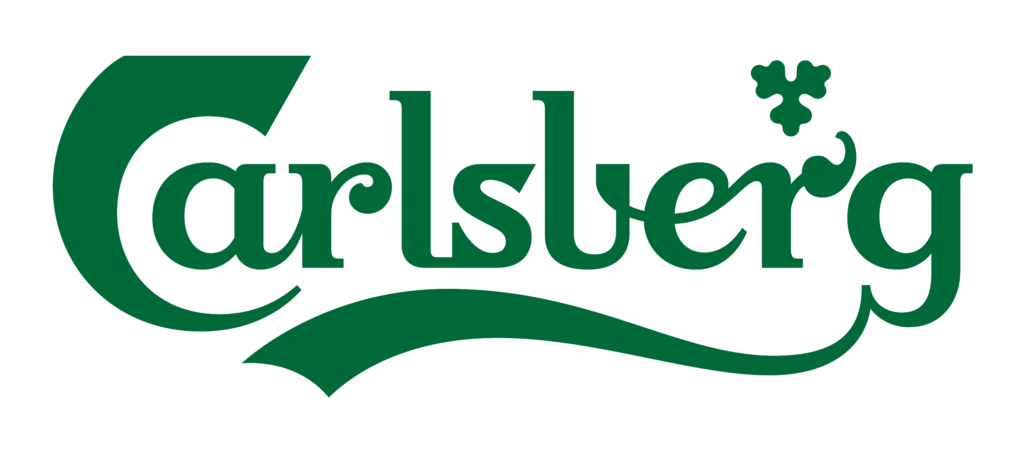
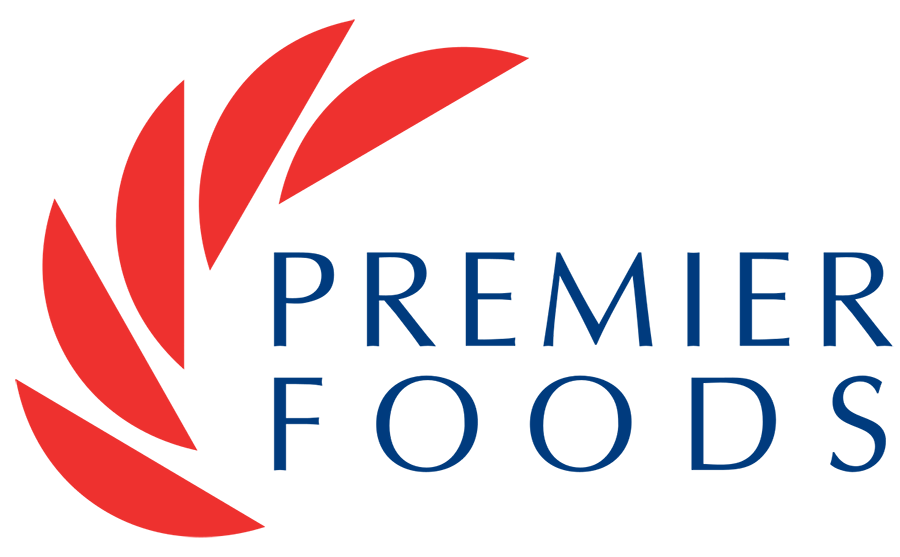
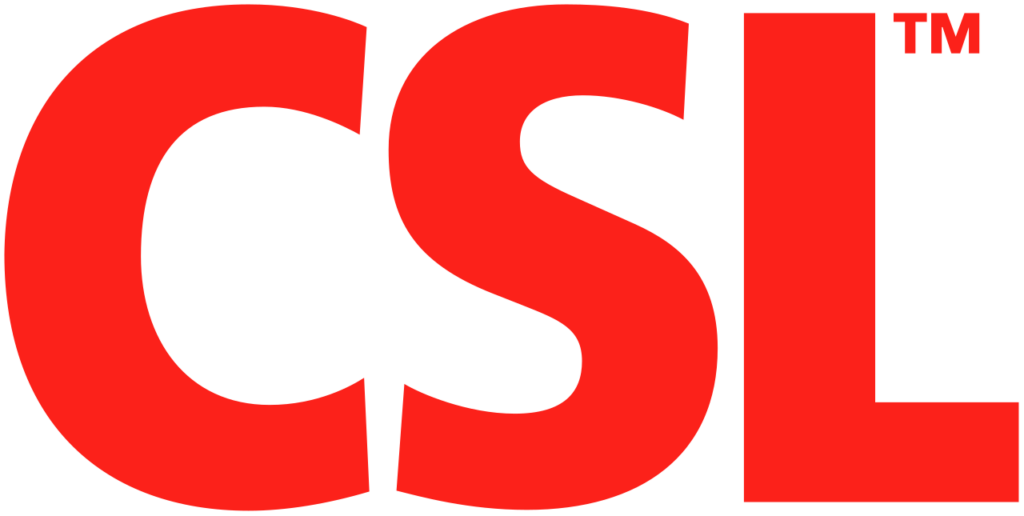
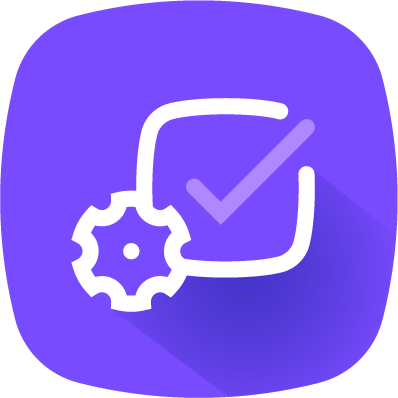
World Class Manufacturing
Accelerate, scale and sustain operational excellence
Zaptic connects frontline workers to the information and tools they need to drive continuous improvement.
View Challenge